


ABOUT US
Ride the crest of the Wolcott wave and find out why so many people use Wolcott Water Systems, Inc. for all their water treatment needs.
We are one of a select few who are factory authorized suppliers for Dow Chemical, Rohm and Haas Ion exchange resins. Selling worldwide, Wolcott gives you freedom to expand your business. We have access to the world’s largest supply of ion exchange resins. Our fully stocked, almost 2 acre warehouse will make Wolcott your first choice for water treatment supplies.
We carry Amberlite, Ambersep, Amberjet and Dowex (manufactured in the United States) resin, as well as all support products needed in the industrial water treatment market. These products include RO membranes, filter media, sand, gravel, activated carbon, and anthracite. The large volume of inventory also gives us the ability to offer the very best pricing and speedy delivery.
Wolcott has offered superior water treatment sales since 1928. We are committed to providing excellent service to all the industrial water treatment markets. We celebrate the spirit of small business by offering flexible, fast and friendly service. Wolcott Water Systems is a women-owned and operated business centrally located in Missouri.
Our industry leading engineers provide quality technical support. We offer many services, including resin analysis, and evaluation. Contact us. We would appreciate a chance to show you how our great service can benefit you.

1928
160
23
1
Year Established
Years of Combined Experience
International Countries Serviced
Strategic Centralized Location
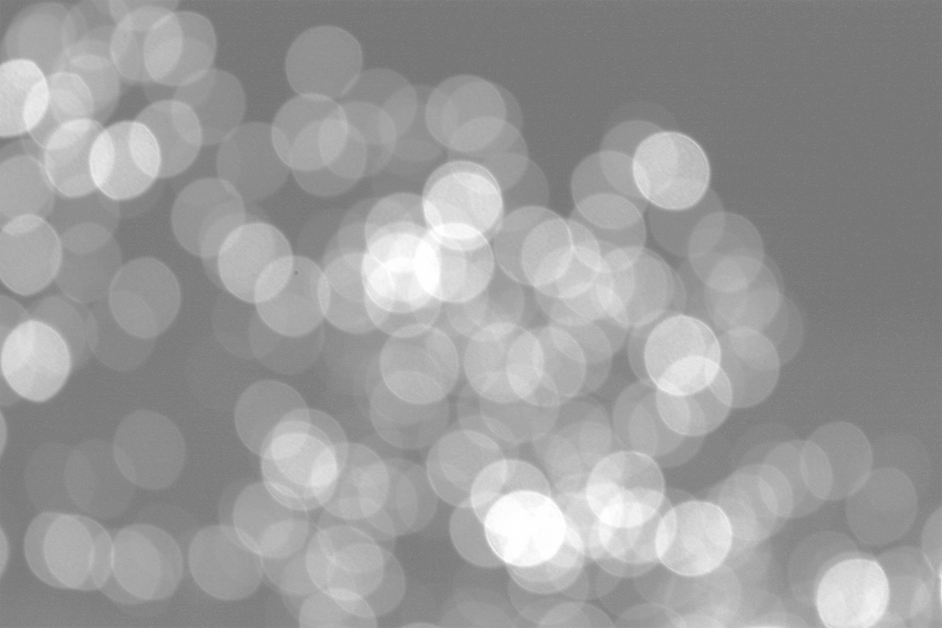
PRODUCT CATEGORIES


SERVICES


Resin Analysis & Evaluation

Technical Support
Technical Support with 160 years of combined experience

Custom Packaging
Various sizes of packaging

Equipment Trouble Shooting
-

2 Acres of Warehousing
Warehousing over 8,000 cf of Resin

Resin Consultation
Resin Recommendation using IXCALC Program
Wolcott Water is available 24/7 for all your emergency water treatment needs.
OUR LEADERSHIP
This is your Team section. It's a great place to introduce your team and talk about what makes it special, such as your culture and work philosophy. Don't be afraid to illustrate personality and character to help users connect with your team.

Visit Us
2007 Wolcott Drive
Columbia, MO 65202, USA
(Mon - Fri 8am - 6pm CST)
Contact Us
